Ceramic And Porcelain Tile Manufacturing
Porcelain tile has been crafted across the globe for thousands of years. Today, updates in design and manufacturing technologies have changed porcelain tile dramatically, making it more durable, easy- ... Read More
HOW PORCELAIN & CERAMIC TILE ARE MADE
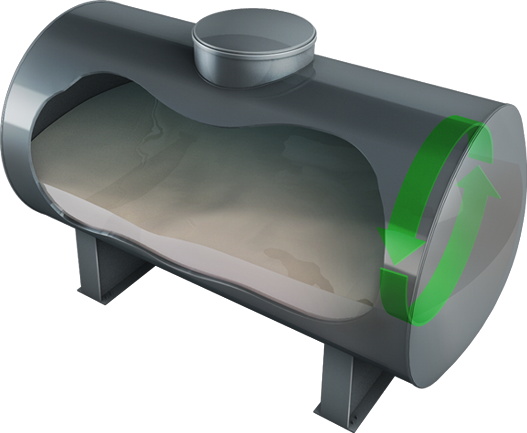

The Magic Begins
Water and raw materials are mixed until a sand-like consistency is reached. Recipes vary slightly, resulting in variations in color, texture, or other characteristics of the tiles. The raw materials used typically include feldspar, clay, silica sand, and other additives.
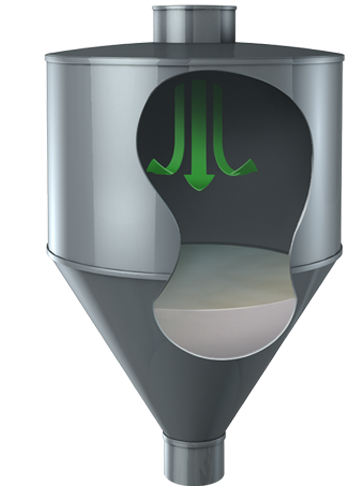

Getting the Perfect Consistency
In this next step, a spray dryer is used to remove excess moisture from the mixture until the perfect consistency is achieved. A spray dryer is a specialized equipment that utilizes hot air to evaporate the water, leaving behind a well-balanced mixture ready for the next stage.
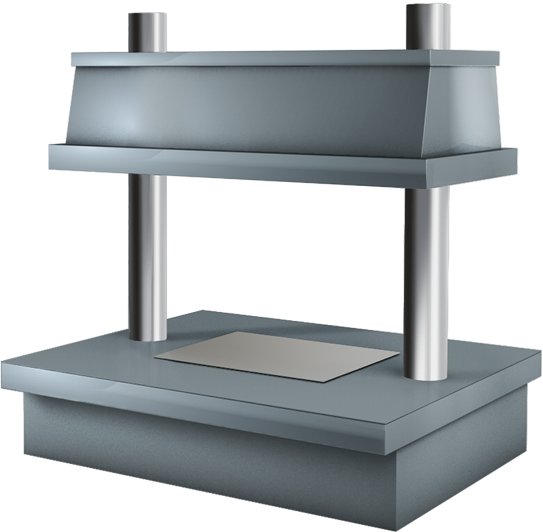

Creating the Tile Body
Now, the porcelain and ceramic mixtures are pressed to form the tile bodies. Each type of tile uses a specially designed punch to shape and form the body, known as Greenware. Porcelain tile and ceramic tile have slightly different compositions, with porcelain being denser and more refined.
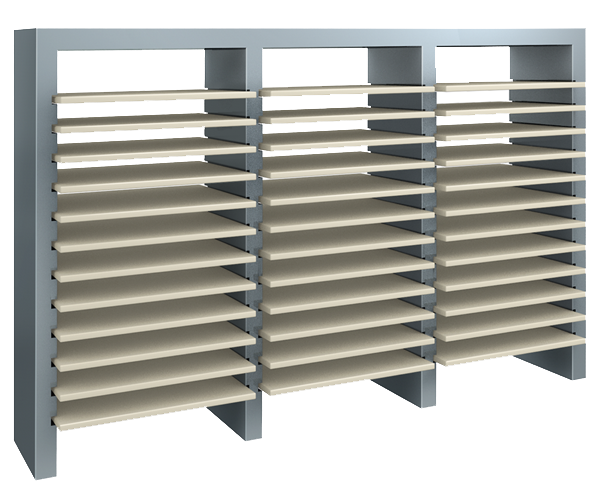

Curing Begins
Before glazing and firing, the Greenware tiles are placed in a dryer to remove moisture, preparing them for the subsequent stages of the process. This step ensures that the tiles are in the optimal condition for further treatment.
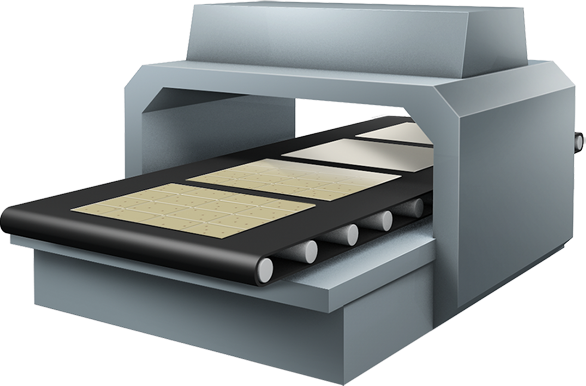

Printing & Glazing
Once the tiles have dried, a state-of-the-art inkjet printer is used to apply the desired pattern and colors to the surface. This advanced printer technology allows for precise and intricate designs. After the pattern is applied, a protective glaze is added to safeguard the tiles and provide a glossy or matte finish, depending on the desired outcome.
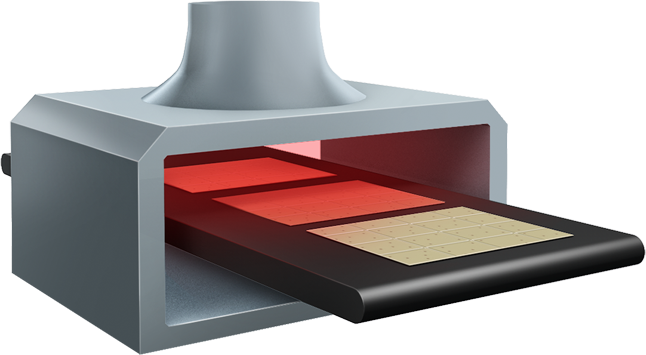

Into the Kiln
The tiles undergo firing within specialized kilns, where they are subjected to elevated temperatures ranging from 2300℉ to 2455℉ (1260℃ to 1345℃) for extended periods. This thermal process eliminates any remaining moisture from the tiles and contributes to their overall strength and quality.